Comprehensive Packaging Equipment Service Solutions for Suppliers
Comprehensive Packaging Equipment Service Solutions for Suppliers
Blog Article
Specialist Product Packaging Devices Service for Seamless Workflow
In today's fast-paced production environments, the relevance of skilled packaging equipment service can not be underrated. Such solutions not only enhance functional performance however likewise play a crucial duty in lessening downtime and making certain product quality. By leveraging knowledgeable professionals for precautionary upkeep and punctual repair services, companies can navigate the intricacies of machinery management (packaging equipment service). The landscape of tools service is evolving, providing both challenges and possibilities that require more exploration. What variables should organizations think about when buying these essential solutions to secure their one-upmanship?
Importance of Professional Service

Additionally, routine maintenance by professionals aids prolong the life expectancy of packaging devices. Expert company are geared up with extensive understanding of different equipment types and industry standards, enabling them to carry out preventative maintenance successfully. This aggressive method not just reduces the likelihood of unexpected break downs yet also improves total functional reliability.
Additionally, professional service can significantly add to conformity with regulative standards. Product packaging devices should abide by rigorous security and quality standards, and expert specialists guarantee that these standards are fulfilled constantly. This not only safeguards item integrity yet likewise protects the firm's credibility.
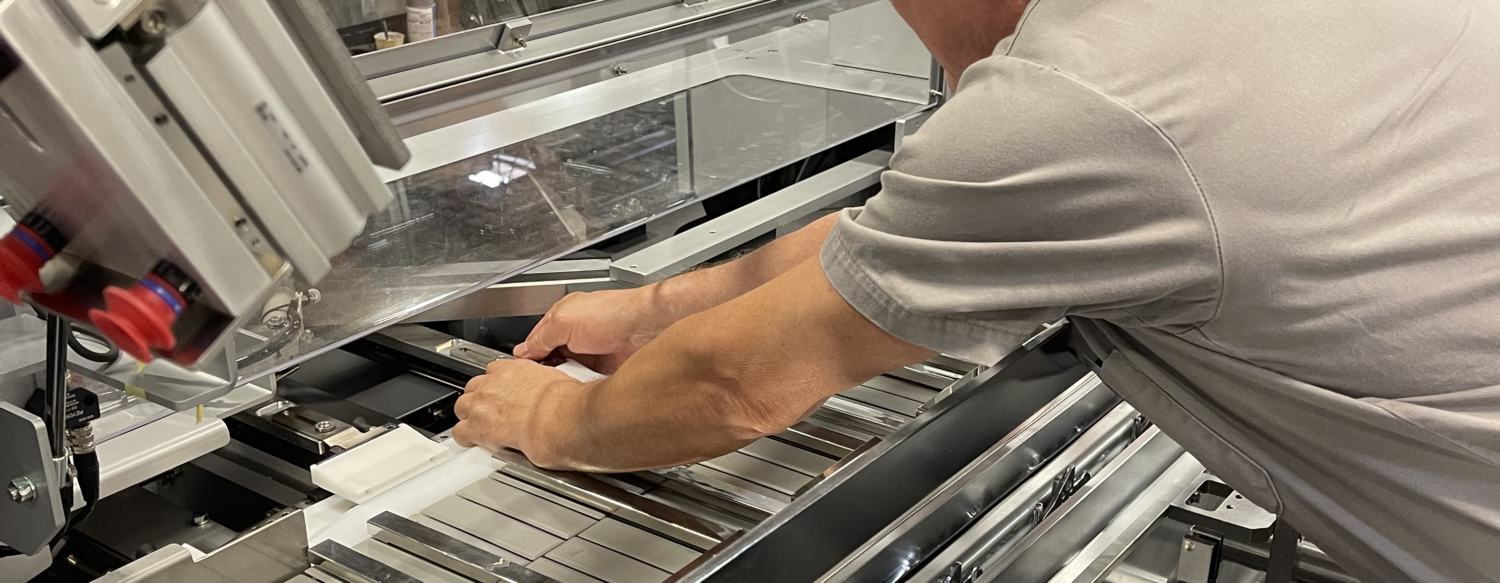
Advantages of Expert Support
Engaging professional assistance for packaging devices not just improves operational effectiveness however likewise delivers a series of fringe benefits that can substantially impact an organization's lower line. One of one of the most notable benefits is the minimization of downtime. Expert technicians can swiftly diagnose and solve issues, making certain that production lines continue to be energetic and minimizing the monetary losses associated with idle equipment.
Additionally, expert support typically consists of preventative maintenance, which can prolong the lifespan of product packaging tools. By frequently servicing equipment, potential issues can be recognized and dealt with prior to they escalate into expensive repairs or replacements. This aggressive approach not only conserves cash but likewise boosts item high quality by making certain that equipment operates within optimum parameters.
Additionally, leveraging the know-how of skilled professionals can cause boosted compliance with market guidelines. These professionals stay upgraded on the most up to date requirements and can direct companies in executing ideal practices, therefore preventing possible legal responsibilities.
Sorts Of Product Packaging Devices Solutions
When it comes to packaging tools solutions, businesses can select from a selection of options customized to satisfy their details demands. These solutions normally drop into a number of classifications, each developed to enhance operational efficiency and decrease downtime.
Preventative upkeep services concentrate on regular inspections and upkeep jobs to make sure that devices operates smoothly and lowers the chance of unforeseen break downs. This proactive approach can expand the life expectancy of machinery and improve performance.
Repair services are vital for dealing with tools breakdowns or failures - packaging equipment service. Experienced technicians detect the problems and perform essential repair services, ensuring that the equipment is brought back to optimum working problems promptly
Installment services are critical when introducing brand-new packaging tools. Specialists manage the configuration, making sure that the machinery is integrated correctly into existing lines and features as intended.
Educating services supply team with the needed skills and knowledge to run equipment successfully. This training can cover everything from fundamental procedure to advanced troubleshooting.
Last but not least, seeking advice from solutions provide critical insights into maximizing packaging processes, assisting businesses determine locations for renovation and execute finest practices. In general, picking the right mix of these solutions can considerably improve product packaging procedures.
Key Attributes to Try To Find
What important characteristics should organizations consider when selecting packaging devices solutions? Expertise and experience are vital. Service providers with a tried and tested track record in the sector can provide invaluable insights and options customized to certain functional demands. In addition, the schedule of thorough assistance solutions, consisting of installation, upkeep, and troubleshooting, ensures that companies can count on timely assistance when concerns emerge.
One next page more secret feature is the versatility of solution offerings. A company that can adapt to developing company demands, such as adjustments in manufacturing volume useful site or product packaging specs, will contribute in maintaining performance. Moreover, technology assimilation must be a priority; modern-day packaging tools services should integrate sophisticated modern technologies, such as automation and real-time surveillance, to improve efficiency.
Lastly, track record and client feedback need to not be forgotten. Involving with reviews and case researches can give a more clear photo of a service copyright's dependability and quality. By considering these crucial attributes, companies can make informed choices that will sustain their packaging operations and add to general success.

Buying Long-Term Success
Investing in lasting success in product packaging devices services calls for a critical technique that prioritizes sustainability and scalability. Firms need to concentrate on picking equipment that not just satisfies current functional needs yet additionally suits future development and technological developments. This insight decreases disturbances and enhances overall effectiveness.
An essential component of this investment is the regular maintenance and service of equipment. Establishing a proactive service routine minimizes downtime and prolongs the life expectancy of equipment, eventually causing set you back financial savings. Partnering with experienced company makes certain that the tools is maximized for efficiency, hence keeping high manufacturing criteria.
In addition, incorporating cutting-edge innovations, official source such as automation and IoT connection, can substantially improve operational capacities. These developments permit real-time monitoring and data evaluation, enabling business to make enlightened decisions that line up with their lasting objectives.
Finally, buying worker training on new technology and best practices fosters a society of constant enhancement. By cultivating a competent labor force, organizations can adapt to transforming market demands and keep their one-upmanship. Inevitably, an alternative technique that encompasses equipment, solution, modern technology, and workforce development placements business for sustained success in the product packaging market.
Conclusion
In final thought, professional packaging tools solution plays a critical role in guaranteeing smooth procedures within manufacturing atmospheres. By prioritizing these services, companies can attain optimal operational effectiveness and expand the life expectancy of their equipment.
Report this page